Material Science in Fast Motion (Ceramic-Wiki)
Before the globalization the ceramic offerings were strongly dependent on local availability of clay bodies. In Germany for example the porcelain industry and craftsmanship were rising mostly next to the kaolin deposits. The kaolin mine in Amberg/Hirschau was responsible for the big companies around Weiden (Selb, Rosenthal). Big clay deposits in Westerwald lead to a still existing pottery focus area. Famous is the Kannebäckerland and the Westerwälder Stoneware. A big driver of ceramic craftsmanship was also the existence of forests, as wood firing was for a long time the only possibility to create durable pottery.
One can roughly distinguish between three types of ceramic. Ceramic, that has been fired around 1000°C is called earthenware. Earthenware is still rather open, can saturate with water and is therefore not frost-resistant. You can identify earthenware easily using a microwave. If you put a watered but outside dry ceramic into microwave, it is getting hot fast. Earthenware therefore is not suitable for tableware in my opinion.
If a clay can be fired to more than 1200°C and are sintering (water absorption less than 3%), the ceramic is called stoneware. Stoneware has a higher density and therefore a higher breaking resistance. This is b.t.w. also a criterion for floor tiles. Stoneware should be seen as standard for tableware today, as there is no possibility for food to migrate into the open pinholes of the ceramic. Hygiene regulations can be kept much easier.
Porcelain is a special type of ceramic, which is sintering dependent from the body from 1250°C. Sintering does imply a gradual glazing of the body itself. This is the reason, why porcelain, if heated close to the sintering point, is getting transparent, which makes the charm of porcelain. Because of its composition, porcelain bodies have only a small plasticity and are difficult to work with, which in the end is responsible for the high price.
Generally speaking, the sintering temperature of the clay bodies is dependent on the additives and is increasing from brown (manganese) to red (iron) to white (pure). From the sintering point onward, the clays become structurally instable. The firing temperature alone is not sufficient to decide about frost-resistance. I measure for all my clays the water saturation and frost-resistance to avoid surprises if the ceramic is in the garden in winter or in the refrigerator.
The degree of added fireclay (grinded clay) does normally not influence the sintering point, but the tolerance of the ceramic in the kiln against thermal variations. Raku ceramic is taken out of the kiln at temperatures around 1000°C, let cool down to approximately 600°C and then smoked in sawdust. Occasionally the ceramic pieces are taken out of the sawdust at around 100°C and then quenched with water. Of course, this is a good application for fireclay additives to avoid deletion of the pieces.
Nevertheless, also stoneware tableware should be put in the cold oven and gain temperature slowly with the oven. And please, put the hot tableware when it comes from the oven not on a cold plate but on a grating.
The addition of fireclay is also very helpful, if you want to create pieces that are larger. The fireclay gives more stability during hand building and throwing and also the drying process has less problems. Drying is in general a topic, as ceramic is drying from outside in and dried clay is more dense than wet clay. So, during the drying phase tensions can be built into the clay and if the clay was not dry enough it will flake during firing as the boiling water from the inside needs a way out.
Slips are whitewashed clay powders, that are applied onto unfired pieces and that connect with the clay body before the biscuit firing. With slips can surfaces of clays with fireclay additions become smoother, one can achieve special reactions with fire or without oxygen and by coloring the slip one can avoid to color the whole clay body.
The biscuit firing is used to make ceramic more stable before further processing, as a chemical reaction has taken place (disappearance of the crystal water a.k.a. quartz inversion at approx. 550°C). The biscuit firing temperature is between 950°C and 1050°C. The ceramic remains porous enough to well accept the liquid glaze, but is stable enough for mechanical decoration steps. The dissolved glaze ingredients can be applied by dipping, spraying and with a brush. As soon as the glaze and the ceramic are dry again, the glost firing can be done until end temperature.
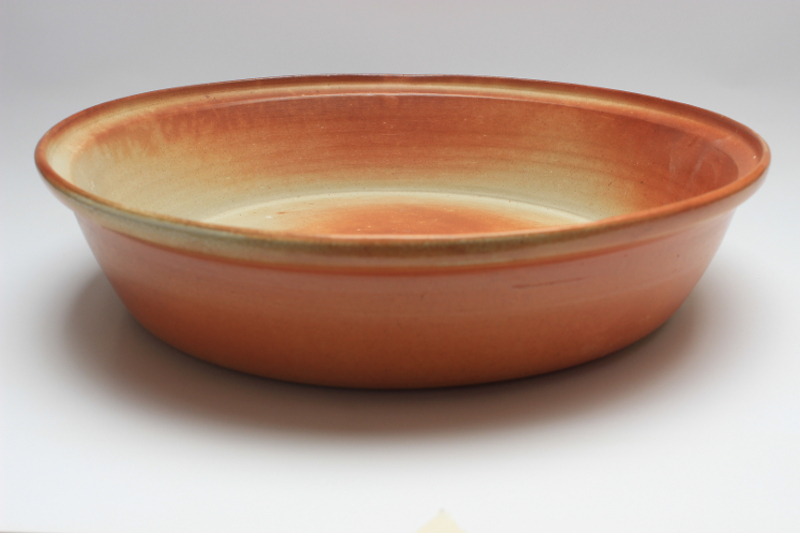
Where has a potter the best possibility to use his own products? Exactly, in his kitchen.

Containers are the little sisters of tea pots, but have more degrees of freedom for decoration and shape.
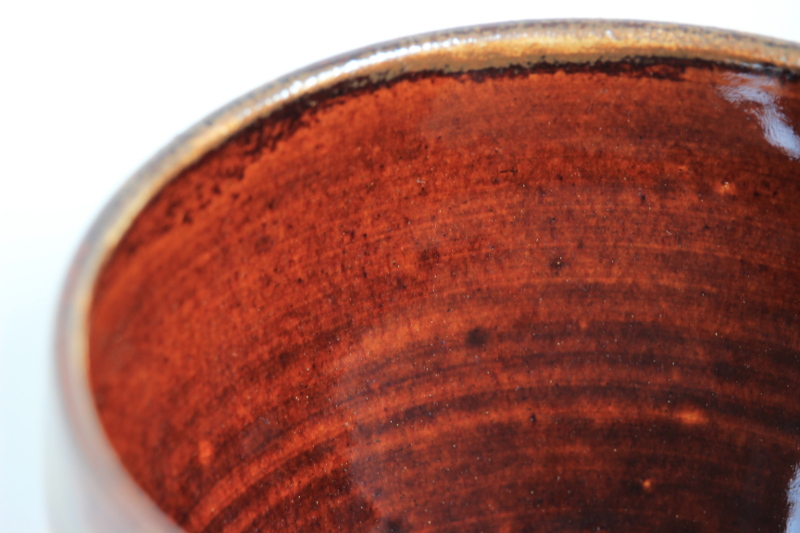
You need more potter experience or advice to realize your ideas? My individual coaching can support you.